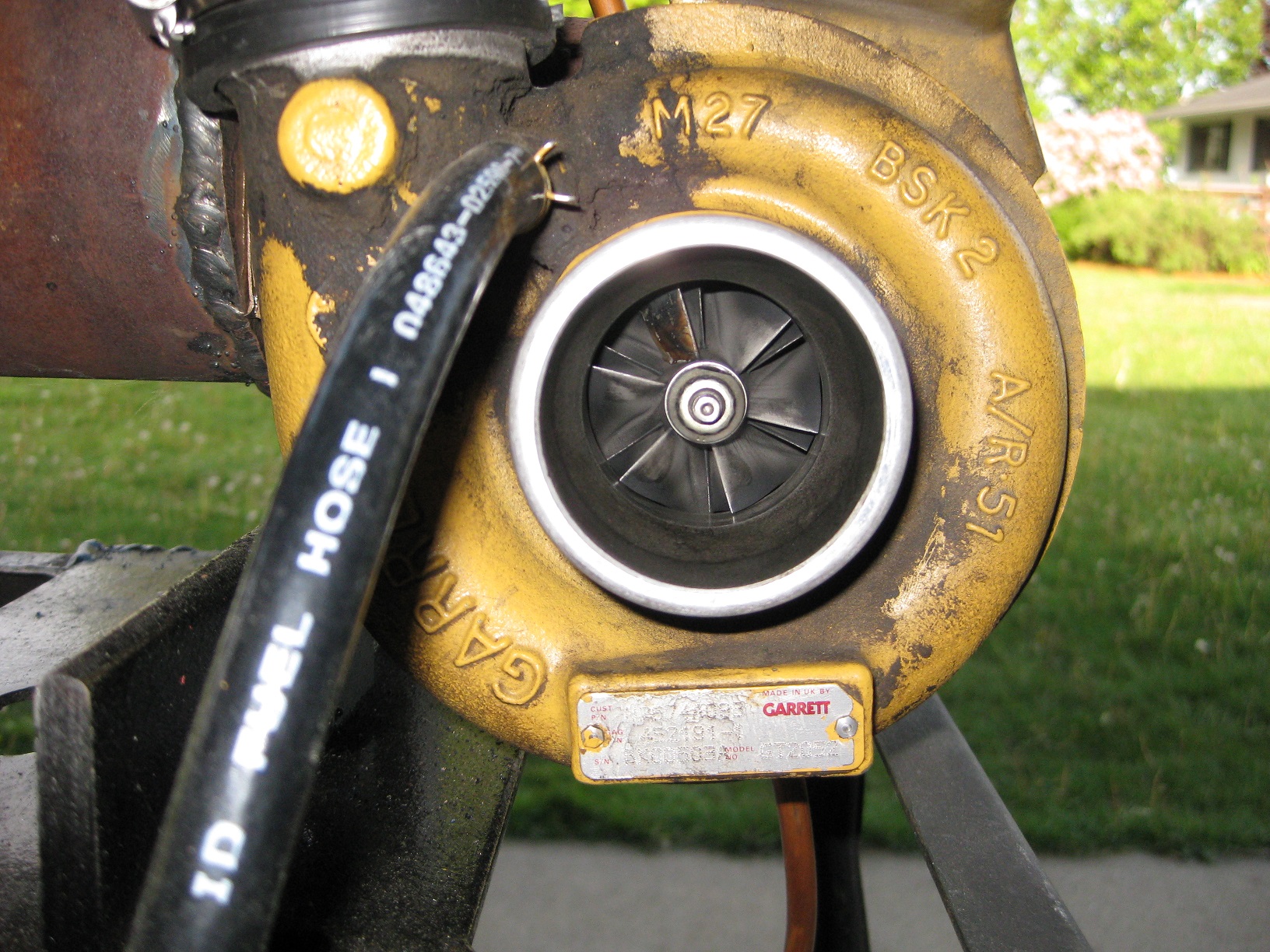
I have always been fascinated with turbine engines. It is amazing that they even work when you examine the relatively few parts inside one. Connect two fans together with a shaft, stuff them in a tube and light a fire in between the fans. That’s all there is to it and they make a fantastic roar when they are running.
This is the basic model of a jet engine. Air enters the intake and is compressed by the 1st fan in the system (the compressor). Fuel is now injected and ignited which expands causing a build up of pressure. The hot gas can not exit through the front, so its only way out is by going out the back where it hits the turbine blade. The turbine blade will spin from the hot gas rushing past it. Notice the turbine is connected to the compressor by a shaft. This shaft powers the compressor so the system is able to keep itself running as long as fuel is ignited. Initial startup requires an electric motor to turn the shaft until the engine starts on its own.
Video of the Engine Starting & running.
1. A Turbo off a car
2. A combustion chamber
3. A Flame Tube
The rest of the parts are small subsystems that are needed for starting, cooling, and monitoring which are discussed later. I had to fabricate everything to fit together so a welder and cutting torch are handy to have.
The Turbine
My turbine is a Garrett GT2052 turbo off a small 4 cylinder diesel engine. This is a pretty small turbo but it will work just fine.
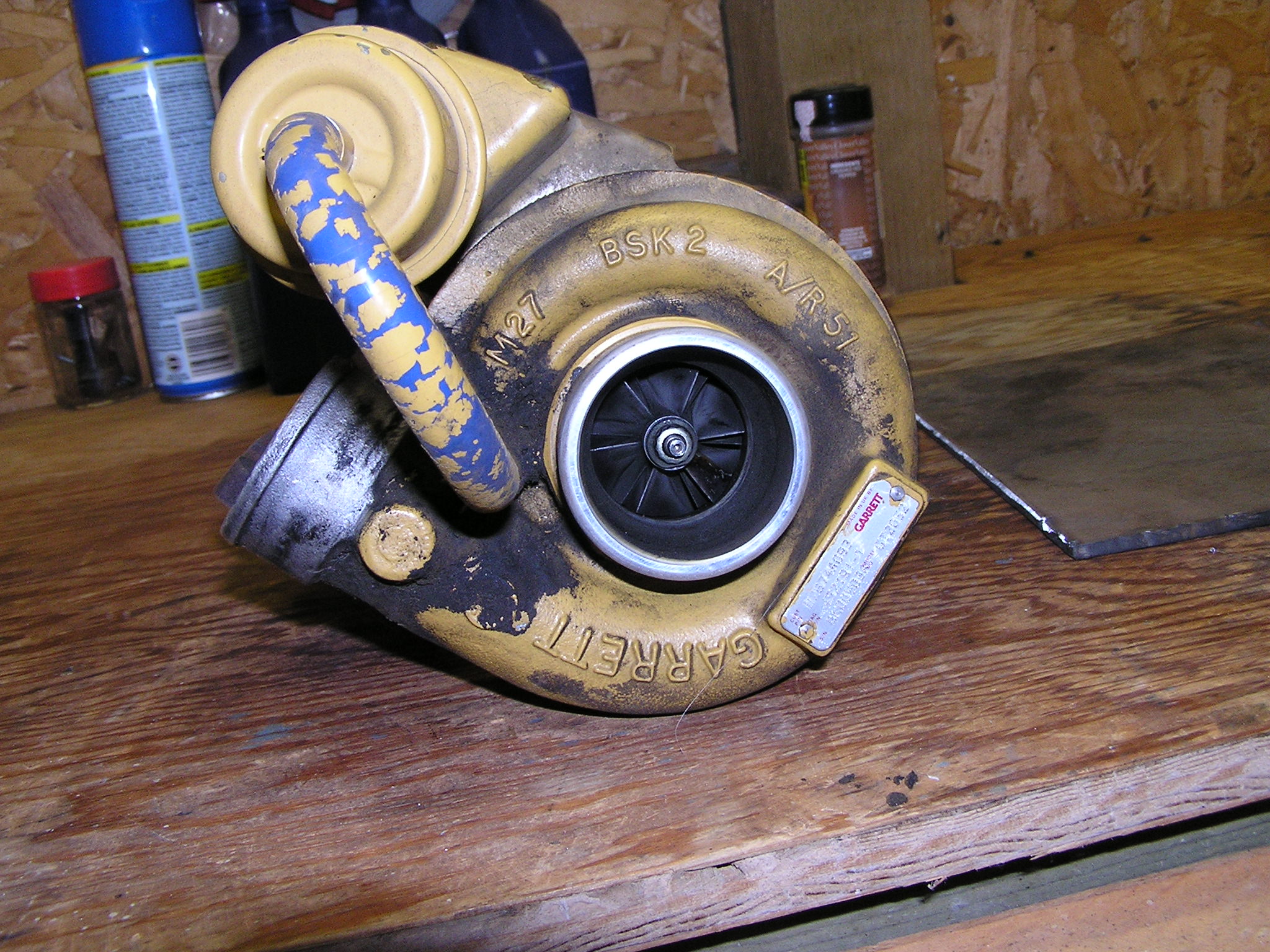
Finding one should not be too difficult. Check your local junk yards or Ebay for a small turbo.
The turbo contains the compressor and the turbine stage of the engine. This works out well because it’s a self contained unit complete with bearings and the shaft. The white cloth is used to plug the oil inlet and exit until I connect the oil pressure system to them.
The combustion chamber was the only part that I had to make from scratch. It is basically a tube inside a tube. The outer tube on my engine is 5 inch diameter. The inner tube is 4 inch diameter. Both tubes are about 12 inches long. The length and diameter do not seem to be a huge factor as long as you have some length to the chamber. I do not know how short it can be and still work.
The tube is made of exhaust pipe as well as the inside tube. I welded a homemade flange on one end so I can bolt a cover on later. The other end has a welded plate with a hole to allow air flow into the turbo.
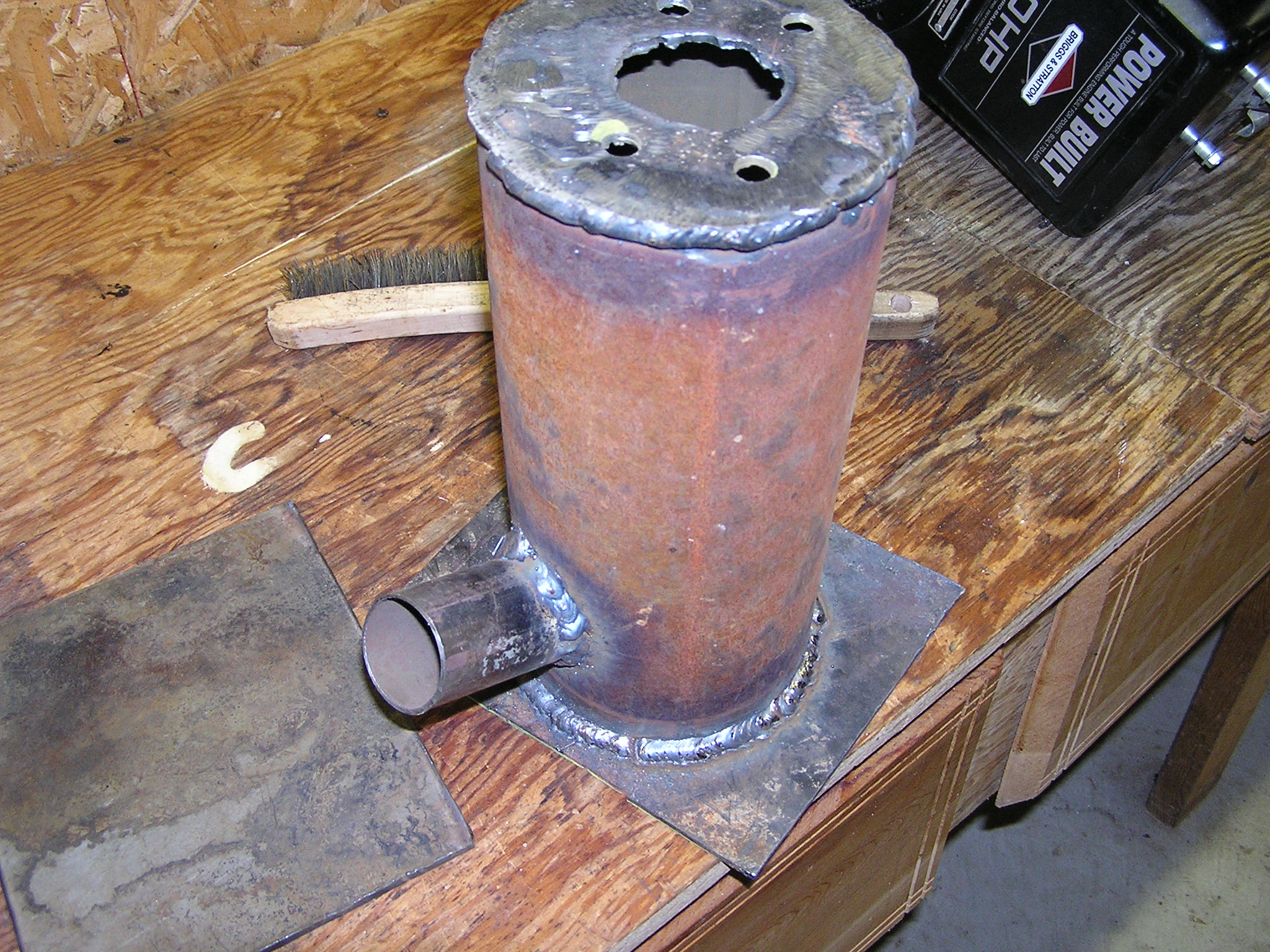
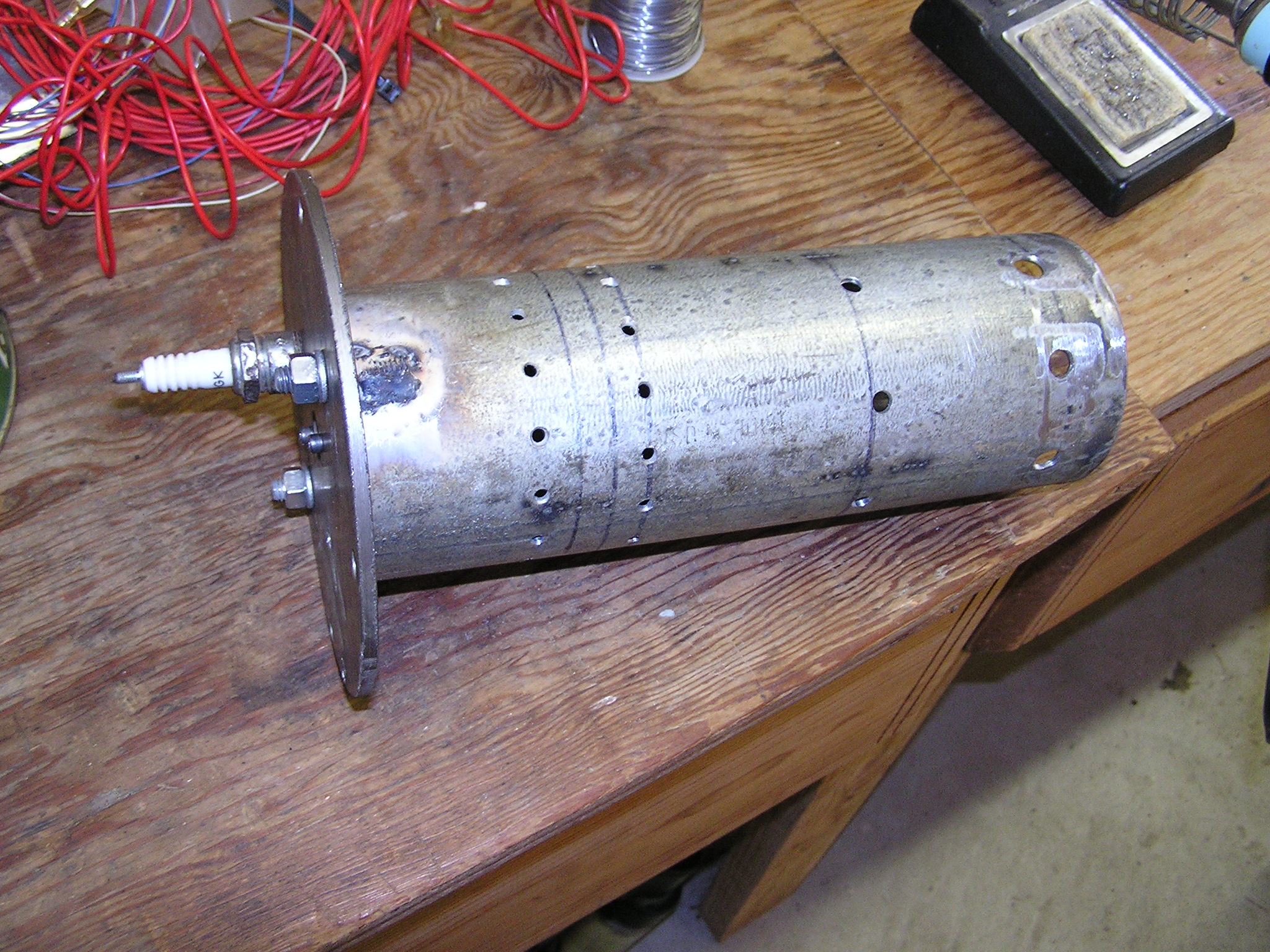
The inside tube also called the Flame Tube is very important. All of the compressed air from the turbo needs to pass through all the small drilled holes in this flame tube. You can see that there is a pattern to the holes.The actual flame will be inside this tube and never touches the outer combustion chamber tube. The rushing vortex of air will help keep things cool. Too many holes will cause your flame to go out so you need to really experiment with the layout. I used a free program called Jet Specs and ended up using the the hole pattern it gave me with great results.
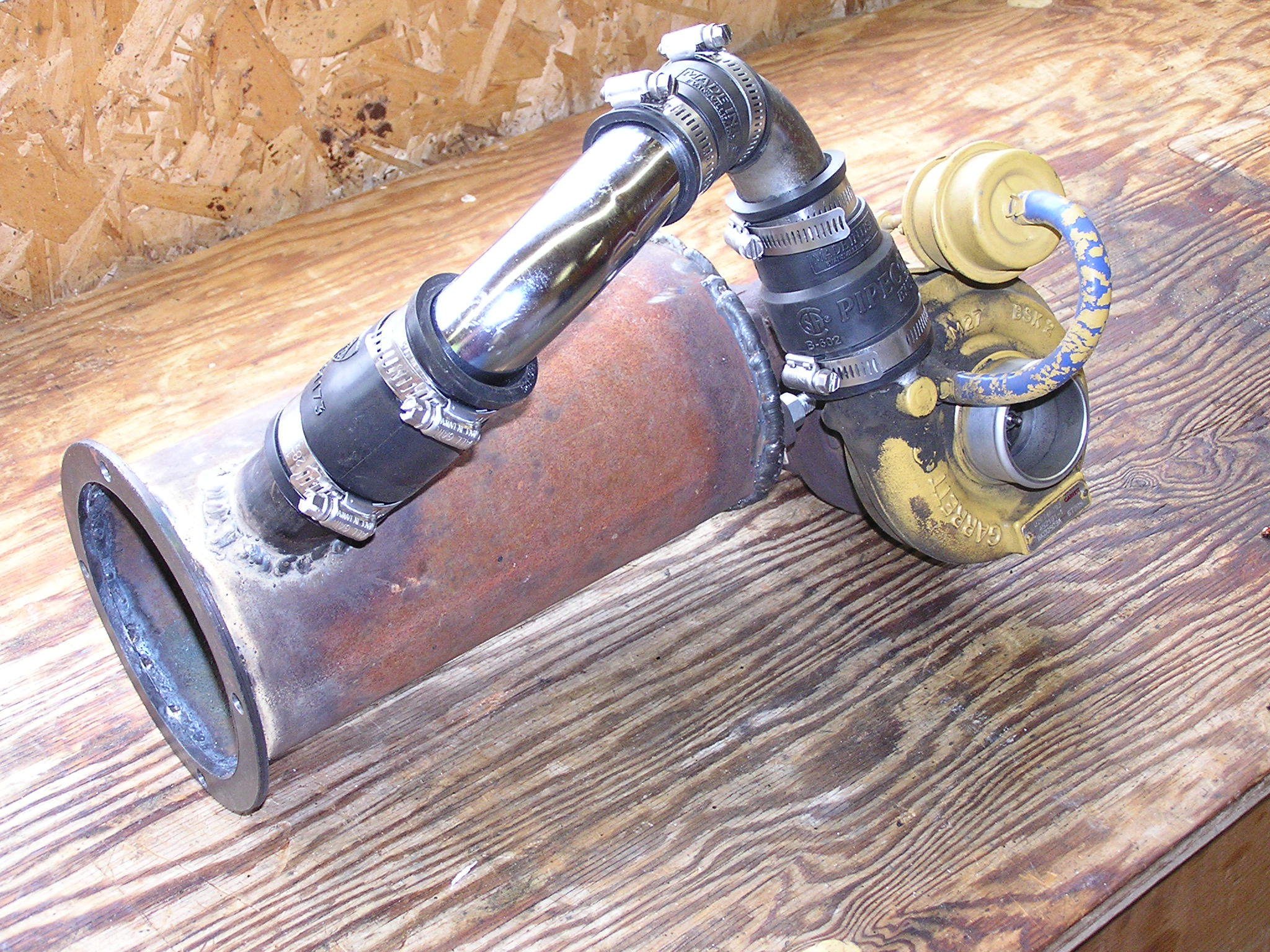
The turbo compressor stage needs to be connected to the combustion chamber as shown. I used plumbing fixtures and rubber plumbing gaskets as show in the picture above.
The engine will run on propane because it is cheap and easy to use. I need a way to ignite the propane gas inside the chamber so I used a standard automotive spark plug. I drilled and tapped a hole so I could attach one as shown. In the very center of the flame tube is where the propane nozzle goes. I used a piece of 1/4 inch copper tube and smashed one end flat to help dissipate the propane evenly and the other end just connects to a 1/4 inch nipple with a compression fitting. I had to play around with different fittings at the hardware store until I got a setup that worked. The flange gets bolted together with 8 bolts and sealed with high temp red silicone gasket.
The only circuit that is needed is something to excite the spark plug. This is needed to ignite the propane so the engine will start. A cheap and easy circuit is to use a power transistor with a 555 timer that will spark the plug when you input 12 volts.
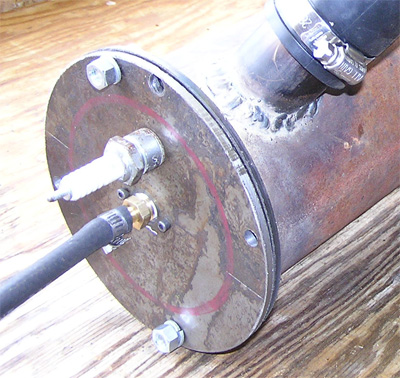
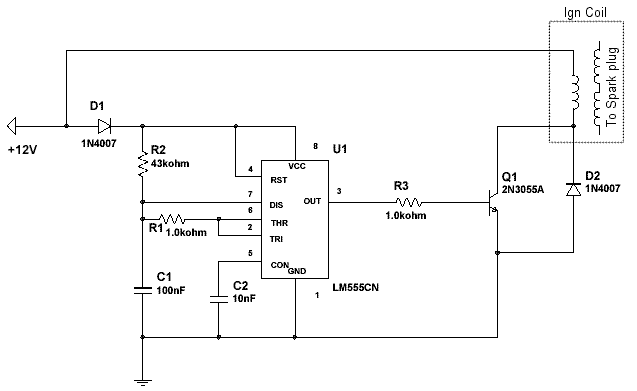

The output of this circuit needs to feed into a ignition coil off a car or lawn mower. The spark plug will connect to the ignition coil.
Gages are not required but I added them to my engine to give me some feedback on what was going on. I added “boost” to measure the air pressure inside the engine. I also added a psi gage for the oil and temperature for the oil. The last gage was just a voltage meter which came with the gage set when I bought it from the automotive store. I want to add engine RPM as well but I have not built that gage yet and I doubt you will find one at a store that will read up to 100,000 RPM. The switch is to turn on the ignition coil and it can be turned off when the engine starts.
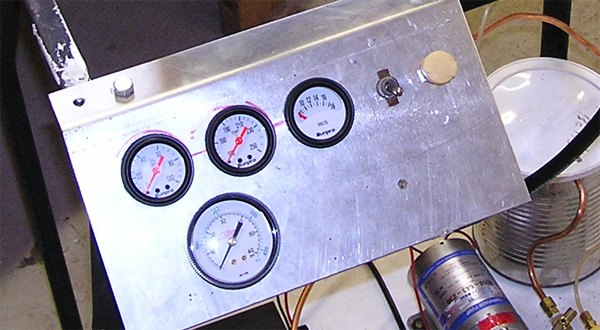
The turbo requires oil pressure for the internal bearings so I had to buy a 12v Shurflow pump that could handle hot oil and I made a small oil resivore out of a coffee can. I used 2 quarts of Synthetic Mobile 1 0w40 oil because the oil will get extremely hot. All the tubing is just 1/4 copper tube with compression fittings. I added a bypass valve so I can control the oil pressure by relieving some of it back into the can. All the copper fittings were obtained at the local hardware store. The black box is just a 12v power supply to power the pump and the ignition circuit. I have used a 12v car battery with great success as well.
The engine throttle is controlled by the propane valve. I used an oxygen regulator with some fittings off of an outdoor grill to adapt it to fit the propane take.
I start the engine by using a craftsman shop vac set to “blow” mode (just switch the hoses around). I force air into the turbo’s intake to get the turbine blades spinning. I then turn the ignition on and then the propane slowly up to 50psi. I usually hear a “pop” sound and the a huge rushing of air. The turbine intake will quickly overcome the shop vac so I remove it and shut it off. I can back off on the propane to 35psi once it starts and it will idle nicely.
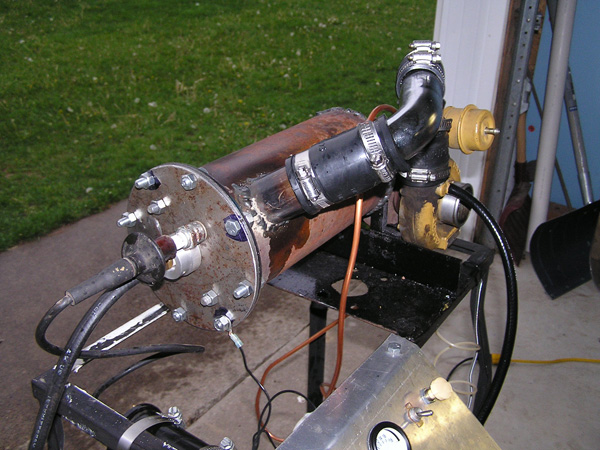
The engine sounds fantastic and is extremely loud. I have to wear earplugs when I am around it.
Hello Mr. Freeman
I want to build a gasturbine too.
But i have a question. from what is that black rubber muff on the outlet of the cold side of the turbocharger?
thanks
Do you mean the black hose off the compressor inlet? That goes to the PSI gage that tells me how much pressure is being created. It’s also called a boost gage.
Hi iam an jet engine builder like u frm india . I wantd to ask u how much pounds of thrust did u get frm ur engine.. . . . .Any1 who wanted to share and discuss abt jet engine projects and want my help in there project mail me Shaj_oconell@yahoo.co.in
Fantastic post.
Mr. Freeman, I want to build the same size as your jet engine, but i don’t know what exact parts I need other than the turbocharger, combustion tube and flame tube. Do you think you could email me the parts you used for your engine. My email is Hammmerhead6473@aol.com
if the 12volts plug sparks 555 time in a minute why you must use the 6 valves.because the normal electricity of 230V it will gives the 28.67 R2 so here you can use the turbain of 12 valves that is dubble of normal which you used.comburshan speed will be less of 23%.
good work.
how will you get some power out of ur
engine. i will love to build something
like that. an organic rankine cycle plant,
useing a turbocharger unit.will it work?
in the ignition circuit , what can i use instead of the power transistor ? it doesn’t seem to be available in the local store
hey guys,
im just wondering in the rear view picture (last picture) what is the silver fitting where the propane intake is that some sort of special butterfly valve so fire does not kick back, the only thing im afraid of is the fire from ignition chamber coming back towards the propane tank :O
If you add some oxygen to the fuel mix it should give the engine more power!!
Hey…just an idea for your tachometer; yes its true you won’t easily find one that runs up to 100KRPM… BUT… why not use a reduction gearing (say, 100:1?) on the input into it, and then use an automotive one? So when it reads 1400RPM, you know you’re putting out 140,000RPM…
I’m no mechanic, but just a thought…
Hi my name is shafiq i am from india . .Bangalore . .I have succesfully built an working jet engine at home using only simple tools. . .If any body wants my plans or any jet engine parts just contact me 09741373279 or email me on shaj_oconell@yahoo.co.in
These turbo charger jet engines dont produce much thrust thats why i made an kj type jet engine plz call me to know more about it and also i sell my homemade jet engines . . . My number 09741373279
Hi there, I was just after a set of plans with some decent details in it. I think I have most of the components ready to go just want to be sure on details before I start welding things up. Would be really appreciated my email is perkozhondacbr@hotmail.com…
My relatives always say that I am wasting my time here at net, but I know I am getting know-how every day
by reading such pleasant articles.
Great Job, well done
I have built a gas turbine using an automobile turbocharger and trying to run it on LPG. Compressed air at about 9 bar is forced into the intake of the compressor and nearly 10,000 rpm are achieved. Unfortunately, the engine does not self sustain.
To which rpm should the engine be brought to make it self sustain? what would be the appropriate way to achieve it?
Hi? Mr. Freeman,
thanks alot man, you motivated me by shared that you v done.
I was so crazy about jet engine but now i wanna do it man, wait and you will see.
Hi!
I’ve been checking thru your projects and are very impressed and have built my own jet engine based on a turbocharger but have some issues with the ignition system. I Believe it’s not as sufficient ås needed. You do not have an exciter/ignition system I could buy from you?
Hi. Hoping you can assist or advise me on my pursuit but basically, I am trying to decide on a build plan for a jet engine of sufficient thrust and minimal weight to be used in a home built aircraft. I will have to make or find almost all parts. The budget for this is about the same amount of money required to maintain a pebble…for an hour…so I will literally be finding what I can in scrap yards and creating as much of it as possible. I know this sounds like an impossible task but, it’s just where I am and like all of us, I keep trying. I have a mild welder and cutting torch, bench grinder, drill press, angle grinder with cut off wheels, etc. so I’m not trying to build this with a rock and a stick. Just looking for a suggestion on buildable, complete plans that cover bearings, type of metal, etc. Anyway, anyone having something constructive to share on this matter, please advise. My Email is DonsFlight@yahoo.com Thank you and good luck to all in your pursuits.
Hi!Mr freeman.Thank a lots for your sharing and I really want to know that yours combustion chamber and ignition system.How can you know complete combustion during engine .
VERY NICE. THANKS.